The BTA® Waste Pulper: Pinnacle of Wet Mechanical Waste Pre-treatment
At the heart of the cutting-edge wet mechanical waste pre-treatment process lies the BTA® Waste Pulper - a pivotal element of every BTA® Hydro-mechanical Treatment. This intricate system has been meticulously designed to achieve three paramount objectives: Fermentable Organic Matter Dissolution and Defibration: Central to the BTA® Waste Pulper's purpose is the swift and comprehensive dissolution and defibration of fermentable organic matter. This crucial step sets the stage for subsequent optimal biogas production.
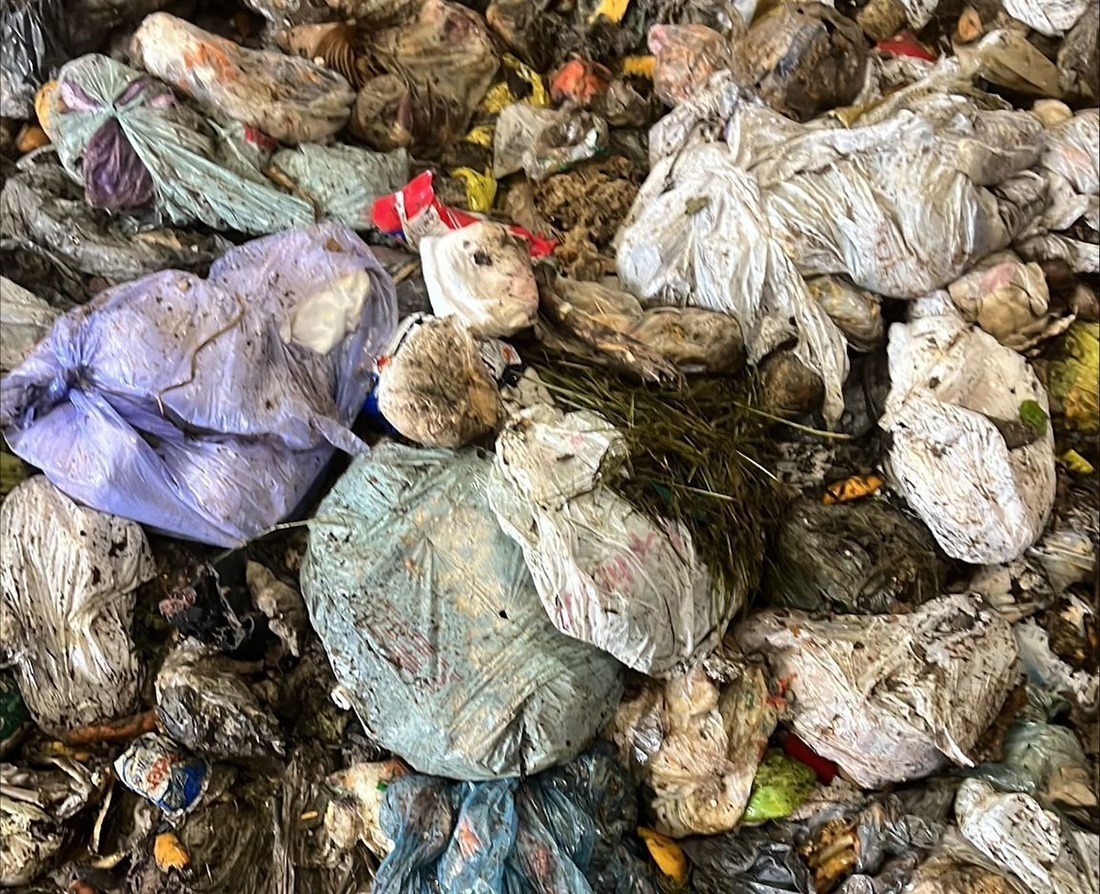
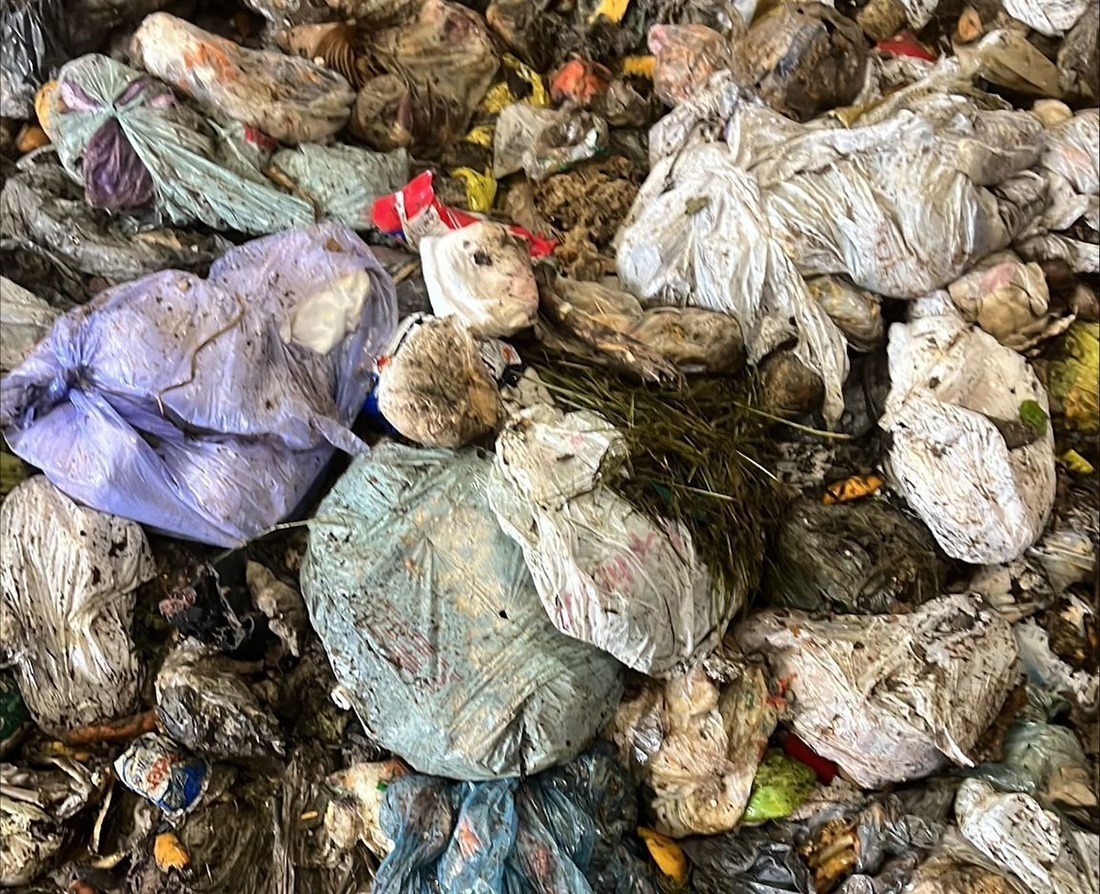
The BTA® Waste Pulper: Pinnacle of Wet Mechanical Waste Pre-treatment
At the heart of the cutting-edge wet mechanical waste pre-treatment process lies the BTA® Waste Pulper - a pivotal element of every BTA® Hydro-mechanical Treatment. This intricate system has been meticulously designed to achieve three paramount objectives: Fermentable Organic Matter Dissolution and Defibration: Central to the BTA® Waste Pulper's purpose is the swift and comprehensive dissolution and defibration of fermentable organic matter. This crucial step sets the stage for subsequent optimal biogas production.
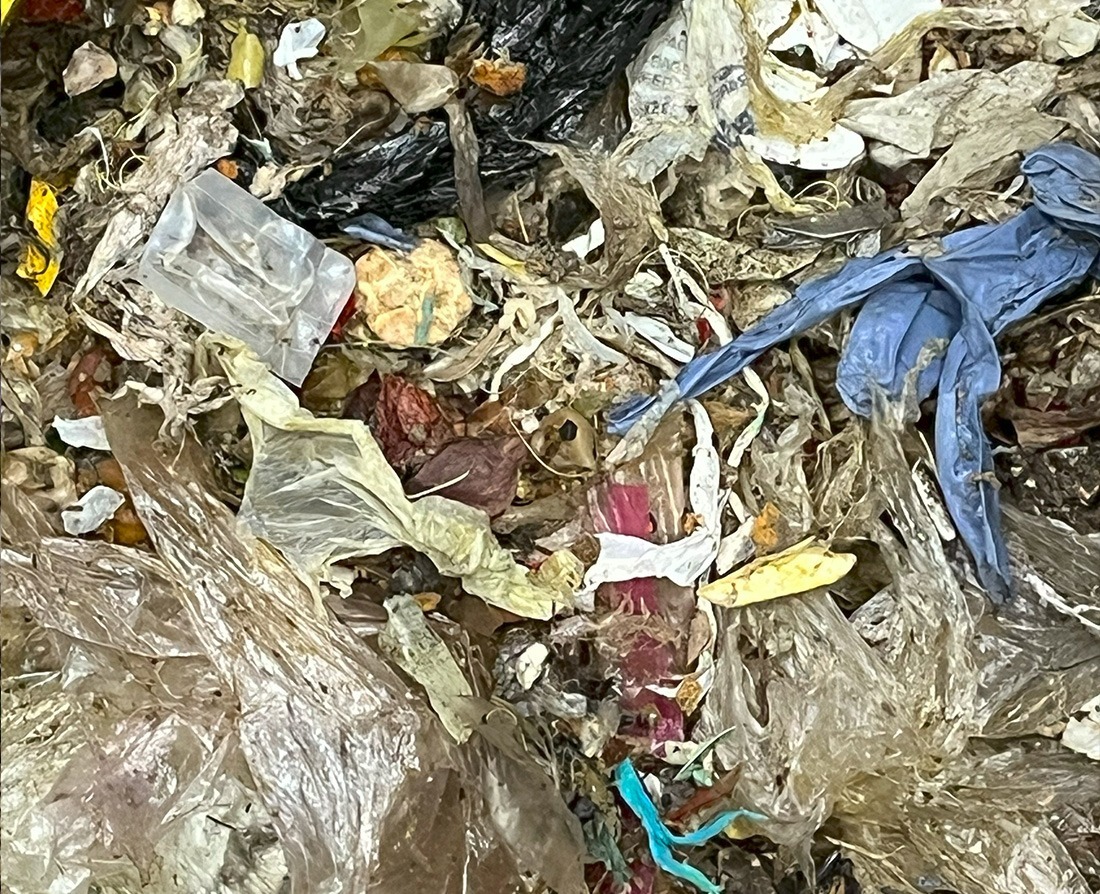
The BTA® Waste Pulper employs the innate principles of buoyancy and sedimentation to meticulously divide the waste mixture into its constituent parts. This intricate process commences with the introduction of a process water mixture to the waste, following preliminary coarse pre-shredding.
However, the BTA® Waste Pulper’s ingenuity goes beyond mere mixing. It harnesses and amplifies the introduced stirring energy to expedite the defibration and dissolution of biomass, achieving both rapidity and efficiency.
The outcome is a smoothly manageable, easily pumpable organic suspension that boasts over 99% of the waste’s fermentable organic fraction.
The resulting organic suspension is skillfully extracted through a perforated screen with a maximum aperture of 10 mm. This suspension, albeit carrying sand and fine sedimentable particles, is then directed to the next stage: sand separation via the BTA® Grit Removal System.
Thorough impurity removal takes place through a sluice, situated at the pulper’s base, for the heavy fraction (metals, bones, glass, stones, batteries, etc.). The heavy fraction journeys through a classifying screw into a designated collection container After the separation of organic suspension and heavy fraction, and the infusion of fresh process water, the light fraction (primarily plastics, wood, textiles, foils, etc.) is delicately extracted using a rake (LRS Rake) or an external screw (LRS Screw) and is subsequently dispatched to a press. Here, dewatering reduces its moisture content to approximately 35-40%.
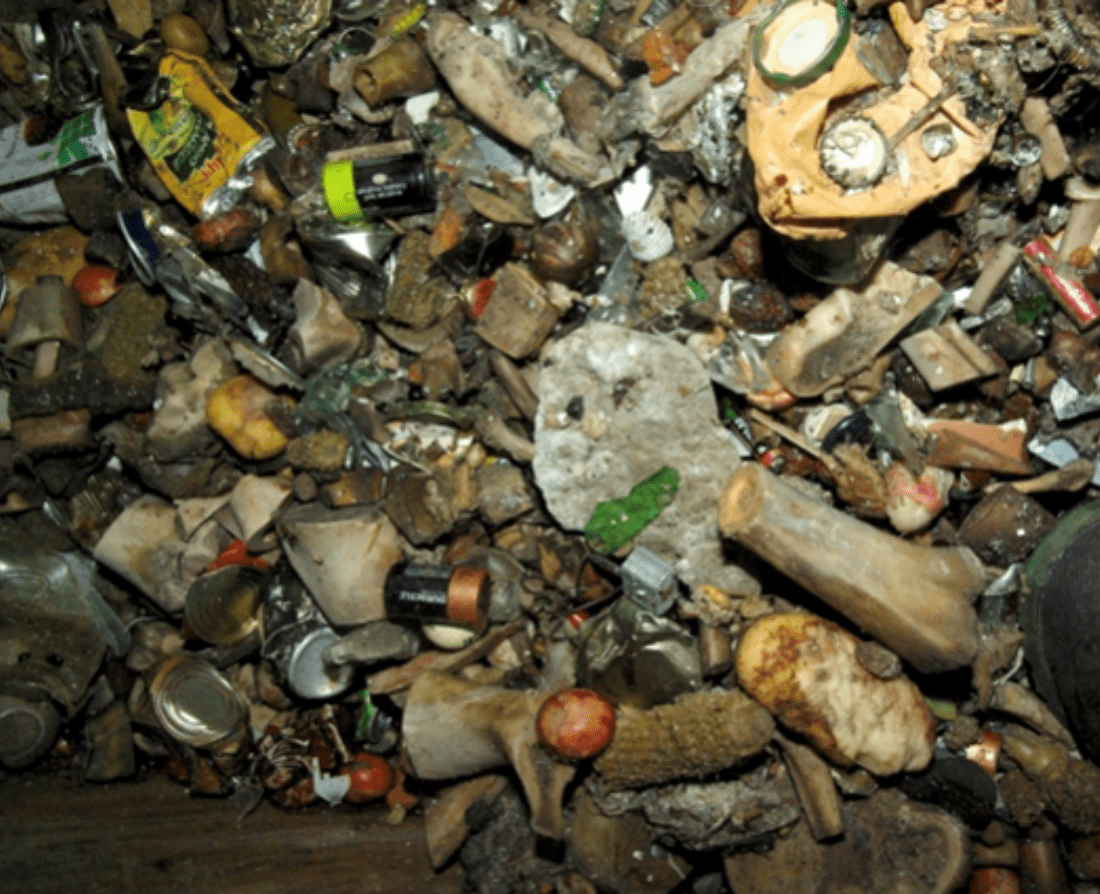
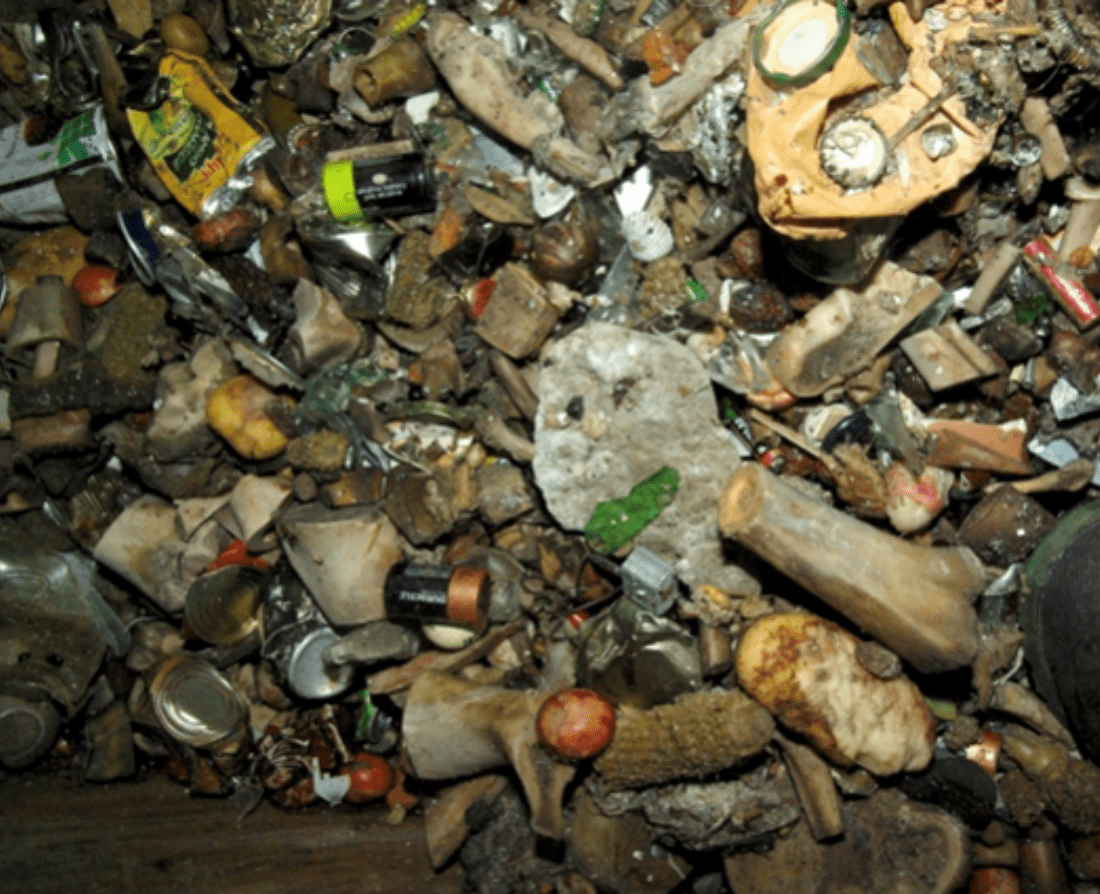
Thorough impurity removal takes place through a sluice, situated at the pulper’s base, for the heavy fraction (metals, bones, glass, stones, batteries, etc.). The heavy fraction journeys through a classifying screw into a designated collection container After the separation of organic suspension and heavy fraction, and the infusion of fresh process water, the light fraction (primarily plastics, wood, textiles, foils, etc.) is delicately extracted using a rake (LRS Rake) or an external screw (LRS Screw) and is subsequently dispatched to a press. Here, dewatering reduces its moisture content to approximately 35-40%.
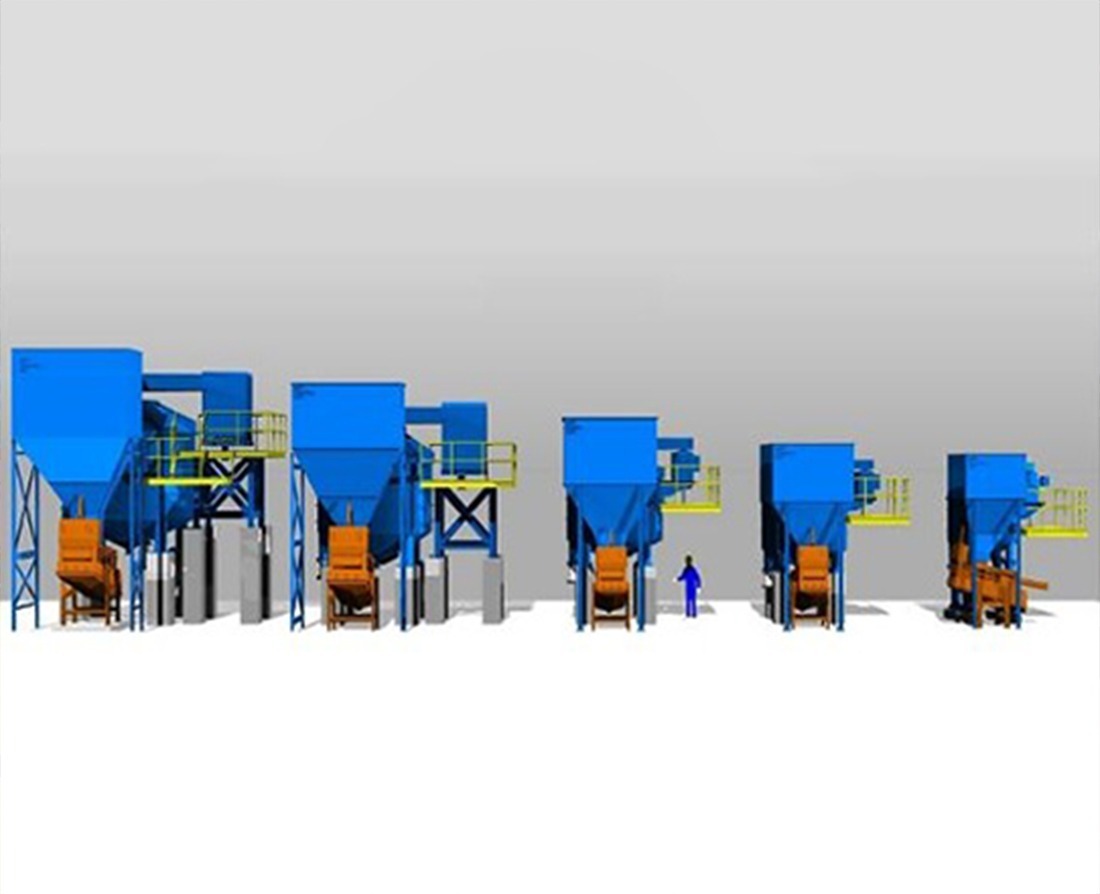
What sets the pulping process apart:
Resilient Contamination Handling:
Its unparalleled capability to manage contamination levels of up to 50% redefines efficiency in waste processing.
Impervious to Hazardous Contaminants:
With the ability to withstand contaminants that could otherwise damage equipment, like large steel pieces or stones, the BTA® Waste Pulper sets new standards.
Preservation of Plastics:
Unlike traditional methods that fragment plastics, the BTA® process prevents fragmentation, reducing contamination in the pulp and minimizing AD system wear.
Amplified Surface Area:
The defibring action leads to an organic suspension with a larger surface area, favoring efficient digestion processes.
Unmatched Organics Catchrate:
The process’s meticulous contamination and plastics washing yields the highest “organics catchrate.”
Versatility across Diverse Waste Categories:
From medical waste to pet-derived residuals, the BTA® Waste Pulper accommodates an extensive spectrum of waste materials.
Exceptional Reliability:
Systems installed in 1994 continue to operate seamlessly, a testament to the BTA® Waste Pulper’s robustness.
Uninterrupted Full Automation:
Fully automated and operational 24/7, the system requires no manual labor, ensuring consistency and reliability.
The BTA® Waste Pulper stands as an emblem of excellence, embodying innovation, efficiency, and reliability in waste pre-treatment. Its ability to handle a wide array of contaminants, preserve plastics, and optimize organic matter digestion makes it a cornerstone of waste processing. With BTA and CCI as partners, the BTA® Waste Pulper emerges as an industry vanguard, upholding the commitment to precision engineering and advanced technology. After the separation of organic suspension and heavy fraction, and the infusion of fresh process water, the light fraction (primarily plastics, wood, textiles, foils, etc.) is delicately extracted using a rake (LRS Rake) or an external screw (LRS Screw) and is subsequently dispatched to a press. Here, dewatering reduces its moisture content to approximately 35-40%.
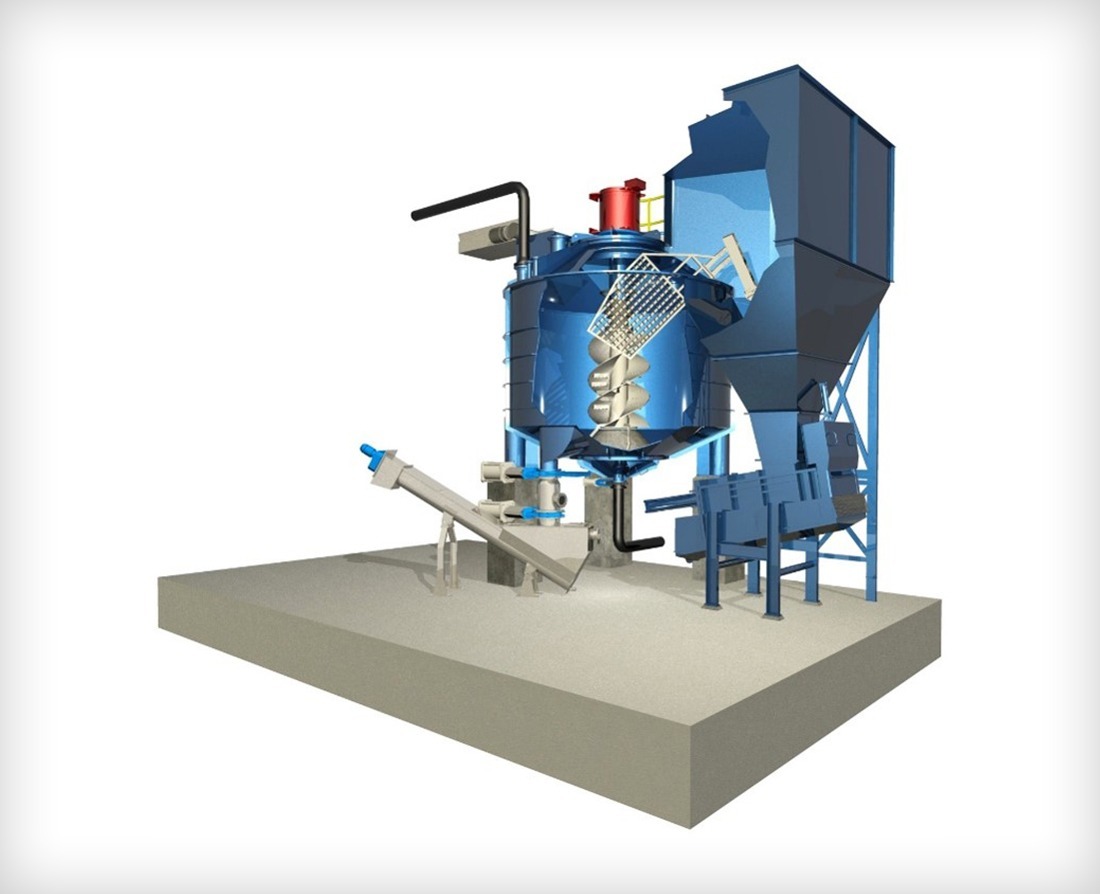
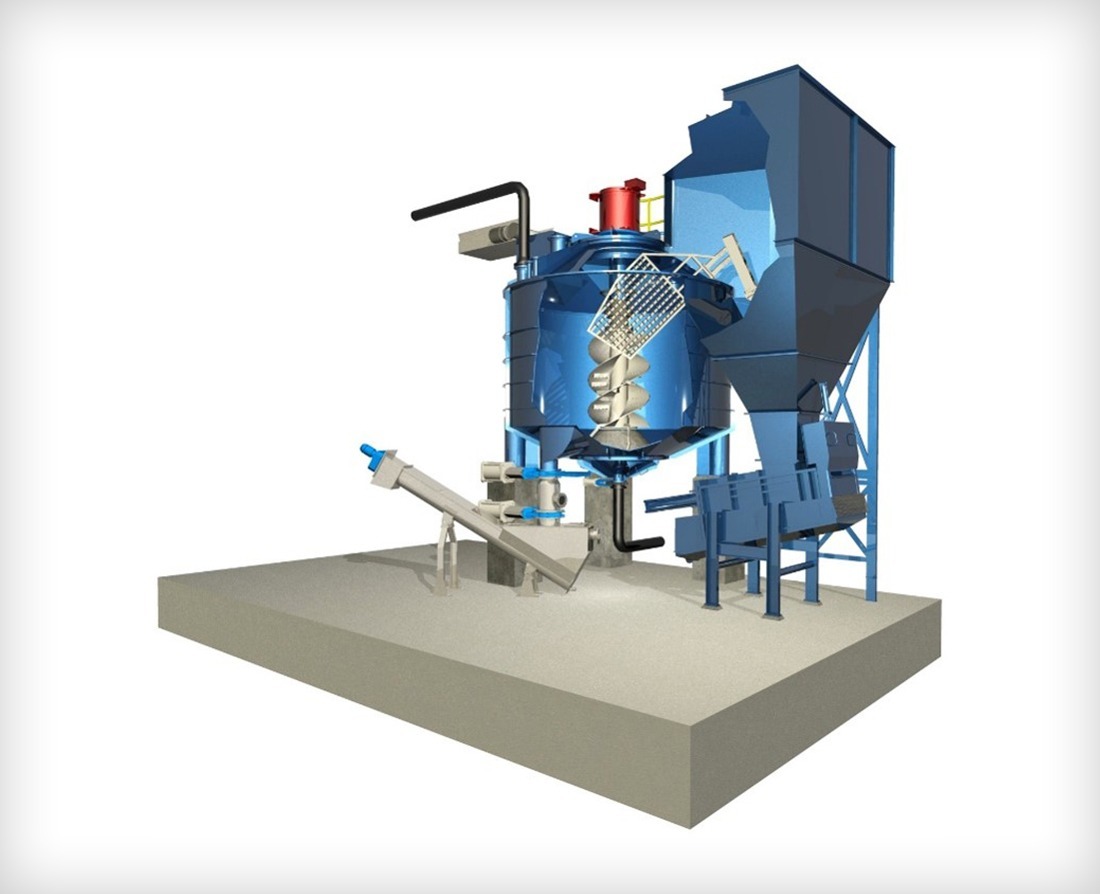
The BTA® Waste Pulper stands as an emblem of excellence, embodying innovation, efficiency, and reliability in waste pre-treatment. Its ability to handle a wide array of contaminants, preserve plastics, and optimize organic matter digestion makes it a cornerstone of waste processing. With BTA and CCI as partners, the BTA® Waste Pulper emerges as an industry vanguard, upholding the commitment to precision engineering and advanced technology. After the separation of organic suspension and heavy fraction, and the infusion of fresh process water, the light fraction (primarily plastics, wood, textiles, foils, etc.) is delicately extracted using a rake (LRS Rake) or an external screw (LRS Screw) and is subsequently dispatched to a press. Here, dewatering reduces its moisture content to approximately 35-40%.